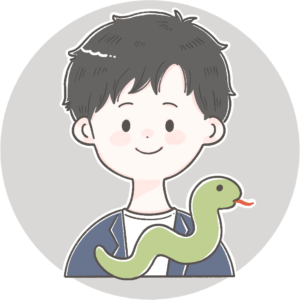
ここでは、主にデータ分析BIツールを導入した企業の、業務改善に成功した活用事例をご紹介いたします。
この記事を読むと分かること
- データ活用事例①ヤマハ株式会社 PDCAサイクルの高速化に成功
- データ活用事例②マツダ株式会社 新帳票基盤で生産性の向上に成功
- データ活用事例③富士通アイ・ネットワークシステムズ株式会社 作業者の人数・残業を減らすことに成功
- データ活用事例④パナソニック株式会社 多くの製造管理指標の可視化に成功
- データ活用事例⑤Pasco 時間管理や配置⼈員の最適化に成功
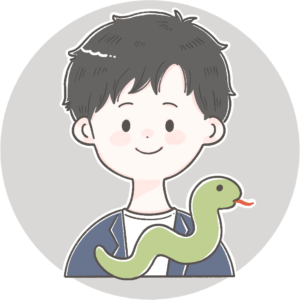
是非最後まで楽しんで読んでいただければ幸いです!
データ活用事例①ヤマハ株式会社 PDCAサイクルの高速化に成功
楽器事業、音響機器事業、電子部品事業などを手がける、ヤマハ株式会社。
データ分析ツールを導入する前のヤマハでは、Excelベースの実績情報しかありませんでした。
さらに複数の現場リーダーが実績入力をするため、データ型や表記方法などが異なり、集計や分析のたびに修正する手間がありました。
また、集計に時間がかかるため、経営層への報告にタイムラグが発生します。
現場で毎日起こるトラブルに対応したくても、遅れが発生してしまうのが課題でした。
そこでデータ分析ツールを導入し、データ分析ツールそのものを報告書代わりにしたため、今まで約50時間かけてExcelで作成していた月次報告書の、作業負担をゼロにすることに成功します。
また、データ分析ツールに加え、ヤマハ独自で開発した実績入力システムを導入したことにより、月次集計していた生産実績を、リアルタイムに自動集計できるようになりました。
こうしてデータを早く集計できるようになり、PDCAサイクルを早く回せるようになりました。
(参考)https://www.wingarc.com/product/usecase/96.html)
データ活用事例②マツダ株式会社 新帳票基盤で生産性の向上に成功
乗用車やトラックの製造、販売などを行っている自動車メーカー、マツダ株式会社。
マツダではアプリケーションシステムごとに様々な帳票ツールを使用しているため、全体の整合性を取るのが難しい状態でした。
また、定義やオーバーレイが各プラットフォームのプログラムでコーディングされている帳票があり、開発やメンテナンスに多くの手間を費やしていました。
帳票システムが複雑なため、ノウハウがブラックボックス化していきます。
放っておくと製品依存から脱却できないリスクがありますし、システムを扱える技術者が退職をしてしまった場合、蓄積された専門的な技術を後継できなくなる恐れもあります。
そこでデータ分析ツールを導入し、帳票基盤の再構築したことにより、各拠点や業務領域ごとに散らばっていた帳票ツールやデータを統合することに成功しました。
結果、基盤運用の負荷やサーバー台数を減らし、生産性を向上させました。
(参考)https://www.wingarc.com/product/usecase/183.html)
データ活用事例③富士通アイ・ネットワークシステムズ株式会社 作業者の人数・残業を減らすことに成功
ネットワークを支えるサービスやプロダクトを提供している、富士通アイ・ネットワークシステムズ株式会社。
データ分析ツールを導入する前は、ライン外からの応援や退出のタイミングを適時に管理できず、人員を過剰に投入してしまったり、逆に人手不足による残業が発生してしまうことが課題でした。
他にも、着荷の作業計画を立てる際に、Excelで集計された予定データをもとに紙に書き出していました。
この作業には一時間弱ほどかかってしまうため、残業してしまう担当者が出てきてしまいます。
データ分析ツールを導入したことで、部品ごとにバラツキがあった検査・入庫作業の作業の平均化を実現できたため、過剰だった人員を把握できました。
そのため、部品の受入検査時に常に配置していた作業者を、3名から2名に減らすことができ、人員削減に成功しました。
また、自動的に最新データが反映されるようになったため、計画作業を大幅に省くことができ、担当者の残業を無くすことができました。
(参考)https://www.wingarc.com/product/usecase/189.html)
データ活用事例④パナソニック株式会社 多くの製造管理指標の可視化に成功
白物家電をはじめ、照明器具、住宅設備などを手がける、パナソニック株式会社。
特定部品の設計を変更した際に連動して、管理工程図や作業指図書が修正されているかどうか確認できる仕組みを作りたいと考えていました。
工場のあらゆるプロセスを、データ分析ツールで統合し一括で管理することで、4M(品質管理のためのチェック要素)の変化点や生産進捗、品質データなど、全25項目にわたる製造管理指標の可視化に成功しました。
これらの情報を製造現場で共有することで、変化点や工程異常に対して即座にアクションを起こせるようになりました。
(参考)https://www.wingarc.com/product/usecase/178.html)
データ活用事例⑤Pasco 時間管理や配置⼈員の最適化に成功
超熟シリーズで有名な、大手製パン会社のブランドであるPasco(運営:敷島製パン株式会社)。
パンそのものはライン生産方式によって作られ、ある程度は集計方法が定まっていました。
しかしライン生産方式以外の作業(原料の出庫・清掃・事務・会議など)については、適切な集計方法が分かっていませんでした。
時間管理や配置人数に関してはExcelで加⼯集計していたため、どうしても時間や手間ががかかってしまいます。
また、日々の業務報告書類は手作業で作っており、タイムラグが生じる要因になっていました。
実際、⽣産⽇報は翌日にならないと配信できない状態でした。
データ分析ツールを導入し、⽣産管理と勤怠管理システム、全⼯場でのデータ集計と加⼯、レポート配信を自動化させました。
結果、時系列やライン、工場などの単位ごとで実績を集計したり比較できるようになり、想定と実績がズレた場合の原因が分かりやすくなりました。
また、⽣産⽇報は各⼯場に定時配信することにより、工場ごとの状況を把握しやすくなったため、異常値がでた場合にすぐ対応できるようになったりと、優先順位が明確になりました。
まとめ
データ分析BIツールを導入した製造業の、業務改善に成功した活用事例をご紹介いたしました。
製造業の中でも製品を多く扱っている企業では、データの数も種類もバラバラになりやすくなります。
特に歴史が長い企業だと、データ分析の基盤が整っていなかったり、現場の感覚に頼ったために技術の継承に悩んだりと、様々な問題を抱えがちです。
ですが、企業によって様々なノウハウが蓄積されているのも確かです。
データ分析を導入すれば、培われた技術をより良く活用できる可能性が生まれるので、積極的に取り入れていってほしいと思います。